Ngày nay, cách phân biệt các loại gỗ công nghiệp: MDF, HDF. MDF, gỗ ép, gỗ nhựa không chỉ giúp bạn hiểu rõ đặc tính của từng loại mà còn giúp tối ưu hóa chi phí và nâng cao giá trị thẩm mỹ cho không gian sống. Vậy có những cách nào để phân biệt các loại gỗ công nghiệp này? Hãy cùng CABINET MASTER tìm hiểu qua bài viết dưới đây nhé!
>>>> BÀI VIẾT LIÊN QUAN NHẤT: Bảng giá ván gỗ công nghiệp phổ biến, tốt nhất
1. Gỗ MFC (Melamine Faced Chipboard – Gỗ ván dăm)
Gỗ MFC là vật liệu phổ biến trong ngành công nghiệp nội thất và xây dựng. Dưới đây là cách phân biệt các loại gỗ công nghiệp – gỗ MFC.
1.1 Phân loại và cách phân biệt các loại gỗ công nghiệp MFC
Dòng gỗ MFC có nhiều loại do có sự khác biệt về thành phần, nguyên liệu cấu tạo. Cụ thể như sau:
- PB là viết tắt của “Particleboard” hay ván dăm PB. Đây là sản phẩm gỗ nhân tạo được sản xuất từ nguyên liệu gỗ rừng trồng ngắn ngày như bạch đàn, keo, cao su. Ngoài ra, PB có độ bền cơ lý cao và kích thước bề mặt rộng. Điều này giúp mang đến sự phong phú về chủng loại để ứng dụng trong ngành công nghiệp nội thất và xây dựng.
- MFC là viết tắt của “Melamine Faced Chipboard”. Gỗ MFC được phủ lớp nhựa Melamine trên bề mặt.
- OSB hay còn gọi là gỗ ván dăm định hướng (Oriented Strand Board). Đây là sản phẩm ván gỗ công nghiệp được tạo ra bằng cách kết hợp vỏ bào với các chất kết dính.
Cách phân biệt các loại gỗ công nghiệp MFC như thế nào? Gỗ MFC là một loại vật liệu được tạo ra từ ván dăm và phủ bề mặt bằng nhựa Melamine. Gỗ này có đặc trưng là bề mặt không mịn, thô ráp. Bên cạnh đó, có nhiều loại cốt gỗ ván dăm khác nhau và được phân biệt bởi màu sắc như cốt trắng, cốt xanh chống ẩm, cốt đen.
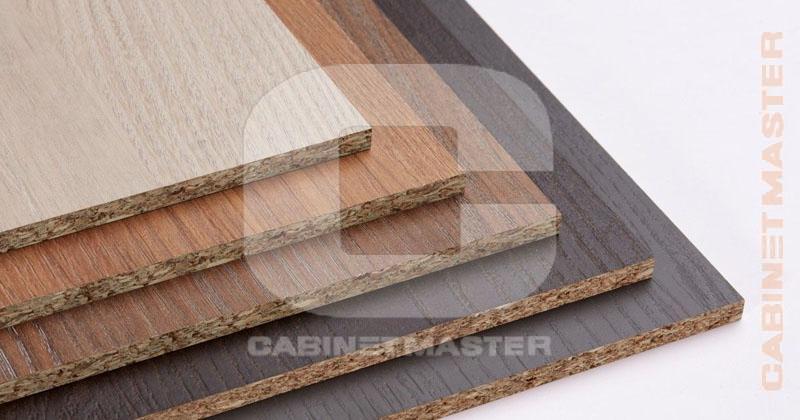
1.2 Nguyên liệu cấu thành
Nguyên liệu sử dụng để sản xuất gỗ công nghiệp MFC bao gồm các loại gỗ rừng trồng có thời gian thu hoạch ngắn ngày như: keo, bạch đàn, cao su. Đây là những nguồn nguyên liệu phổ biến trong ngành công nghiệp gỗ. Đồng thời, các nguyên liệu này được chọn lựa để đảm bảo tính bền và mang lại hiệu suất cao trong quá trình sản xuất gỗ MFC.
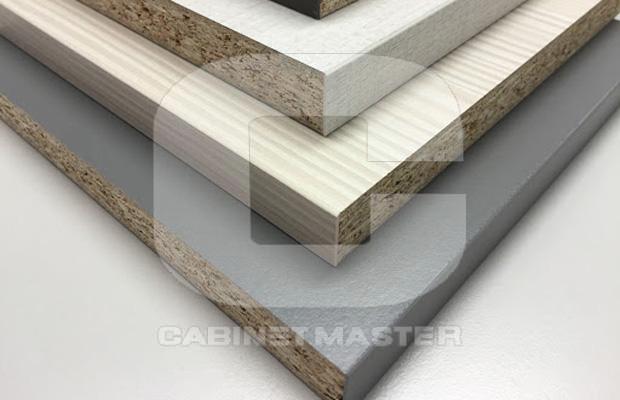
1.3 Quy trình sản xuất
Quy trình sản xuất gỗ công nghiệp MFC bao gồm các bước sau:
- Chế biến gỗ: Gỗ được đưa vào máy băm để chuyển thành các dạng gỗ dăm.
- Kết hợp với keo công nghiệp: Dăm gỗ sau đó được kết hợp với keo công nghiệp. Quá trình này giúp tạo ra một hỗn hợp chất có cấu trúc chặt chẽ.
- Ép cường độ cao: Hỗn hợp gỗ và keo được ép cường độ cao để tạo thành các tấm gỗ với độ dày khác nhau. Độ dày các tấm gỗ thường là 9mm, 12mm, 15mm, 18mm, 25mm và các kích thước khác. (1 ly = 1mm)
- Tráng phủ Melamine: Cuối cùng, bề mặt của tấm gỗ được tráng phủ lớp Melamine. Lớp này không chỉ tạo độ bền và chống trầy xước mà còn giúp sản phẩm chống thấm nước.

1.4 Kích thước
Gỗ công nghiệp MFC có đa dạng độ dày. Tuy nhiên, độ dày phổ biến được sử dụng là 18mm và 25mm. Đồng thời, kích thước tiêu chuẩn của tấm ván MFC là 1220mm x 2440mm.
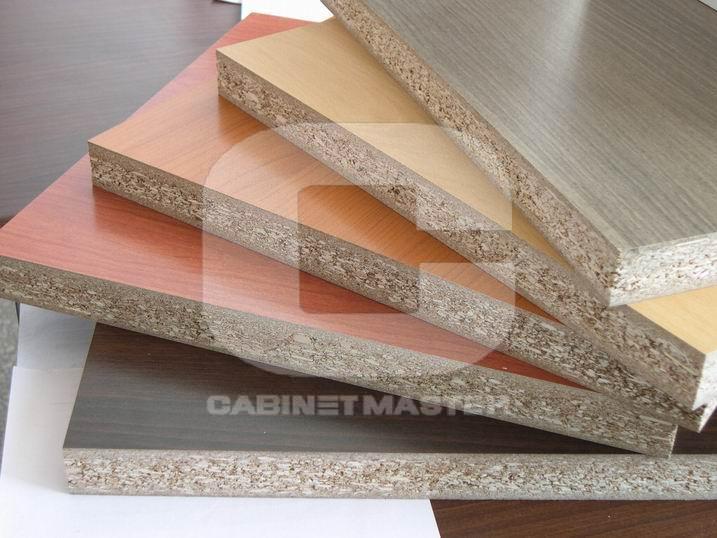
1.5 Ưu nhược điểm
Ứng dụng của gỗ MFC rất đa dạng và đặc biệt là trong lĩnh vực nội thất văn phòng, nhà ở, chung cư, bệnh viện, trường học. Gỗ MFC có những ưu điểm sau:
- Chống cong vênh, bong tróc và ngăn mối mọt tốt.
- Nội thất từ gỗ MFC có tuổi thọ từ 10-15 năm, ít thay đổi chất lượng theo thời gian.
- Khả năng chống ẩm tốt, phù hợp với khí hậu nóng ẩm mưa nhiều của nước ta.
- Khả năng cách âm, cách nhiệt tốt.
- Bề mặt Melamine có bảng màu đa dạng với rất nhiều màu sắc khác nhau.
- Dễ vệ sinh sạch sẽ do bề mặt Melamine nhẵn phẳng, trơn.
- Ứng dụng đa dạng trong thiết kế nội thất, thi công công trình.
- Thân thiện với môi trường đảm bảo sức khỏe người tiêu dùng.
- Giá cả gỗ MFC rất hợp lý.
Nhược điểm của Gỗ MFC như sau:
- Bề mặt không chân thật bằng gỗ tự nhiên
- Khả năng chịu nước thấp. Có khả năng bị bung và hở ván nếu tiếp xúc với nước lâu ngày.
- Khả năng chịu mài mòn không tốt bằng các loại chất liệu khác.
- Hạn chế về độ dày. Bề mặt Melamine (MFC – Melamine Face Chipboard) có độ dày rất mỏng ước chừng 0.4 – 1 zem (1zem= 0,1mm)
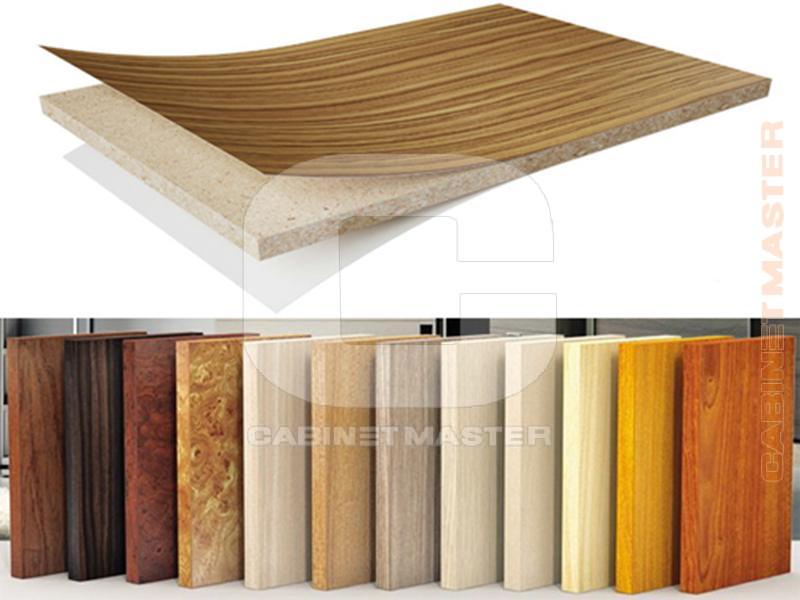
1.6 Ứng dụng
Gỗ MFC được sử dụng rộng rãi để sản xuất các sản phẩm nội thất, bao gồm nội thất văn phòng, nhà ở, trường học, bệnh viện và nhiều nơi khác. Đồng thời, loại gỗ này còn có sự đa dạng về gam màu như đen, trắng, nâu, đỏ, cam, hồng,… mang đến sự hiện đại và tinh tế.
2. Gỗ MDF (Medium Density Fiberboard)
MDF là viết tắt của “Medium Density Fiberboard” trong tiếng Anh, tạm dịch là “Ván Sợi Mật Độ Trung Bình” trong tiếng Việt. Nó thường được sử dụng để chỉ các tấm ván ép có nguyên liệu cấu tạo từ bột sợi với mật độ trung bình. Thực tế, thuật ngữ MDF được sử dụng phổ biến để mô tả ván ép có tỷ lệ nén trung bình và ván ép có tỷ lệ nén cao. Cách phân biệt các loại gỗ công nghiệp, đặc biệt là MDF thường là dựa vào các thông số vật lý như độ dày và phương pháp xử lý bề mặt của tấm ván.
2.1 Phân loại và cách phân biệt các loại gỗ công nghiệp MDF
Gỗ MDF được phân loại theo loại và ứng dụng khác nhau. Cách phân biệt các loại gỗ công nghiệp MDF như sau
- MDF trơn: Thường được sơn PU khi sử dụng.
- MDF chịu nước: MDF trơn nhưng được trộn keo chịu nước trong quá trình sản xuất, phù hợp cho nơi có khả năng tiếp xúc với nước hoặc có độ ẩm cao.
- MDF Veneer: Là tấm MDF được dán một lớp ván lạng Veneer mỏng để hoàn thiện bề mặt. Có thể là Veneer gỗ xoan đào, sồi, Ash, căm xe,… Gỗ MDF Veneer có thể trông giống gỗ tự nhiên và phù hợp cho phong cách nội thất hiện đại, tân cổ điển. Sản phẩm từ gỗ MDF Veneer thường có nét đẹp đặc biệt nhờ vào nét căng phẳng và khả năng ghép nhiều loại vân gỗ khác nhau.
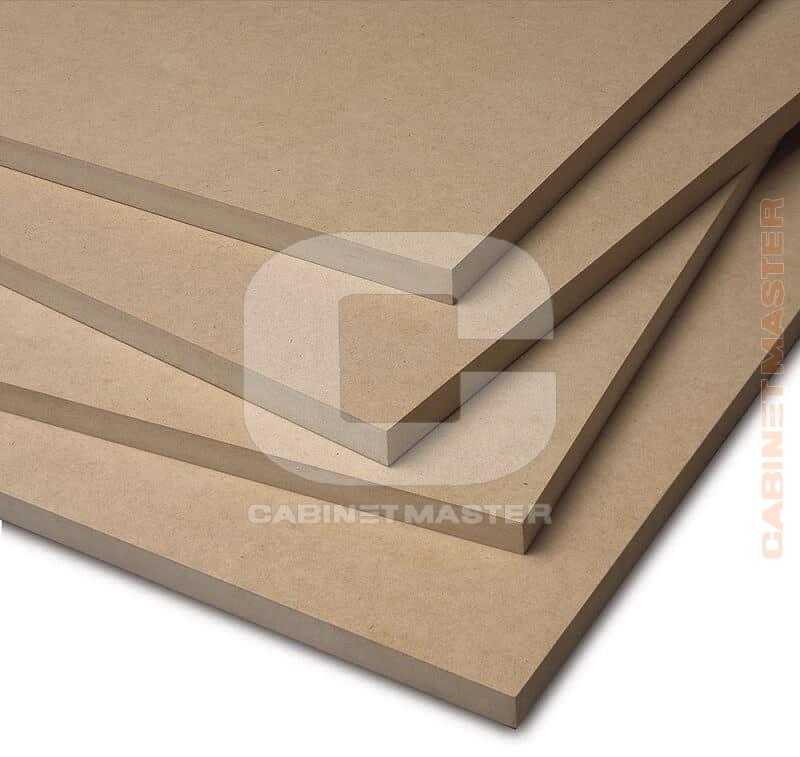
2.2 Nguyên liệu cấu thành
Các thành phần chính của MDF bao gồm:
- Gỗ vụn.
- Nhánh cây được chuyển thành bột sợi gỗ.
- Chất kết dính.
- Paraffin wax.
- Chất bảo vệ gỗ (bao gồm chất chống mối mọt và chống mốc).
- Bột độn vô cơ.
- Keo được trộn để tạo thành kết dính.
2.3 Quy trình sản xuất
- Quy trình sản xuất MDF khô như sau:
Quy trình sản xuất MDF khô bao gồm việc phun keo và phụ gia vào bột gỗ khô trong máy trộn và sấy sơ bộ. Bột sợi được trải ra thành 2-3 tầng tùy theo khổ và cỡ dày của ván bằng máy rải cào. Sau đó, chúng được chuyển qua máy ép có gia nhiệt, thực hiện ép nhiều lần để tạo ra các lớp. Quá trình ép được thực hiện để bốc hơi nước và làm keo hóa rắn. Sau khi ép, ván được xuất ra, cắt bỏ biên, chà nhám và phân loại.
- Quy trình sản xuất MDF ướt như sau:
Trong quy trình sản xuất MDF ướt, bột gỗ được phun nước làm ướt, tạo thành dạng vẩy (Mat Formation). Sau đó, chúng được cào rải và đưa lên mâm ép để ép nhiệt một lần, tạo độ dày sơ bộ. Tấm ván MDF sau đó được đưa vào cán hơi ở nhiệt độ cao để nén chặt hai mặt và làm khô.
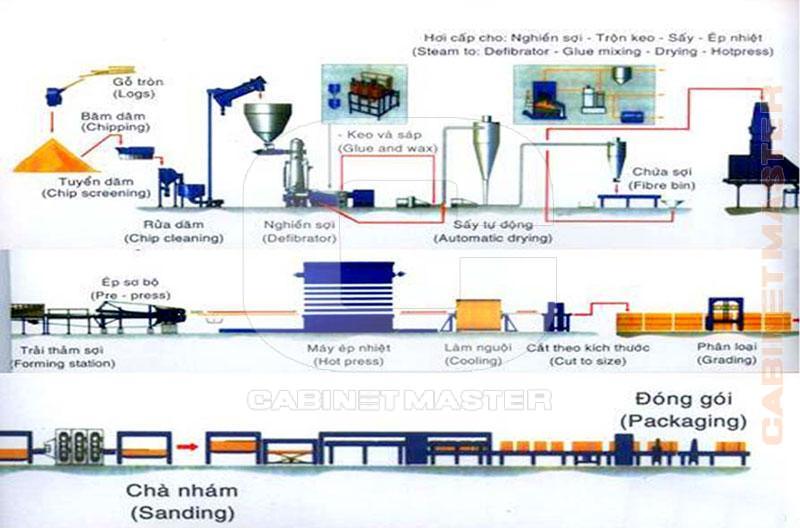
2.4 Kích thước
Hiện nay trên thị trường có 2 loại kích thước gỗ MDF cơ bản là 1220×2440 mm và 1830×2440 mm. Độ dày của từng loại là từ 2,5 đến 25mm.
2.5 Ưu nhược điểm
Ưu điểm của MDF:
- MDF có độ bám sơn cao, đa dạng màu sắc nên thích hợp cho sản phẩm nội thất đòi hỏi nhiều màu sắc như phòng trẻ em, showroom.
- Có khả năng tạo dáng (cong) để đáp ứng yêu cầu của các sản phẩm phức tạp và uyển chuyển.
- Dễ gia công, giúp thực hiện các thiết kế phức tạp một cách dễ dàng.
- Cách âm và cách nhiệt tốt, không bị cong vênh, co ngót và không mối mọt như gỗ tự nhiên.
- Giá thành thấp hơn so với ván dán hay gỗ tự nhiên.
- Cấu trúc đồng nhất, không sứt mẻ khi cắt cạnh.
- Bề mặt phẳng và nhẵn, thuận lợi cho việc sơn hoặc ép các bề mặt trang trí như Melamine hay Laminate.
- Sản xuất ổn định và nhanh chóng, phù hợp cho việc sản xuất hàng loạt các sản phẩm giống nhau, giúp tiết kiệm chi phí và giảm giá thành sản phẩm.
- Kích thước tấm ván lớn, thuận tiện cho việc thiết kế và sản xuất các sản phẩm có kích thước lớn mà không cần chắp nối.
Nhược điểm của MDF:
- Khả năng chịu nước kém.
- Độ cứng thấp dễ mẻ cạnh.
- Hạn chế về độ dày.
- Không thể chạm trổ, đục khắc.
Tuy nhiên, có thể cải thiện nhược điểm về khả năng chịu nước bằng cách sử dụng ván MDF chống ẩm.
2.6 Ứng dụng
Các lớp trang trí như Melamine, Laminate thường được áp dụng lên bề mặt của gỗ công nghiệp MDF để sử dụng trong sản xuất và trang trí nội thất như bàn, ghế, giường, tủ, kệ, cửa… Các sản phẩm nội thất gỗ MDF có thể dùng cho nội thất văn phòng, nhà ở, trường học,…
3. Gỗ HDF (High Density Fiberboard) là gì?
HDF – High Density Fiberboard là loại ván sợi làm từ gỗ tự nhiên, kết hợp với phụ gia khác nhằm tăng cường kết dính cho gỗ. Màu sắc của lõi gỗ có thể là xanh hoặc trắng, không gây ảnh hưởng đáng kể đến chất liệu của lõi gỗ. Cách phân biệt các loại gỗ công nghiệp HDF như sau:
3.1 Cách phân biệt các loại gỗ công nghiệp HDF
Cách phân biệt các loại gỗ công nghiệp HDF: Gỗ HDF có thể dễ dàng nhận biết qua mắt thông qua màu sắc và tính thẩm mỹ của lớp bề mặt. Đồng thời, khi sờ vào, bạn có thể đánh giá được độ cứng, sự mịn màng, tính nhẵn của bề mặt và độ phẳng của gỗ này.
3.2 Nguyên liệu cấu thành
Gỗ HDF được tạo từ 85% gỗ tự nhiên, phần còn lại của HDF bao gồm phụ gia và chất kết dính. Bề mặt của gỗ này mịn, nhẵn, chống ẩm và khá chống trầy xước. HDF có khả năng bắt ốc vít tốt, độ cứng cao và chịu được tải trọng đáng kể.
Ngoài ra, gỗ HDF được áp dụng rộng rãi trong việc làm sàn, cửa đi và các đồ nội thất cao cấp như tủ bếp, tủ quần áo, các quầy kệ văn phòng. Mặc dù giá của HDF cao hơn so với MDF và MFC nhưng HDF mang lại chất lượng và độ bền cao hơn.
3.3 Quy trình sản xuất
Nguyên liệu chính của bột gỗ là gỗ tự nhiên từ rừng trồng nguyên khối. Sau khi được thu hoạch, gỗ được luộc và sấy khô trong môi trường nhiệt độ cao, khoảng từ 1000C đến 2000C. Quá trình này giúp loại bỏ nhựa và làm khô hoàn toàn nước trong gỗ. Bột gỗ sau đó được kết hợp với các chất phụ gia nhằm tăng độ cứng và chống mối mọt. Dưới áp suất cao, khoảng 850-870 kg/cm2, bột gỗ được ép lại để tạo thành tấm gỗ HDF.
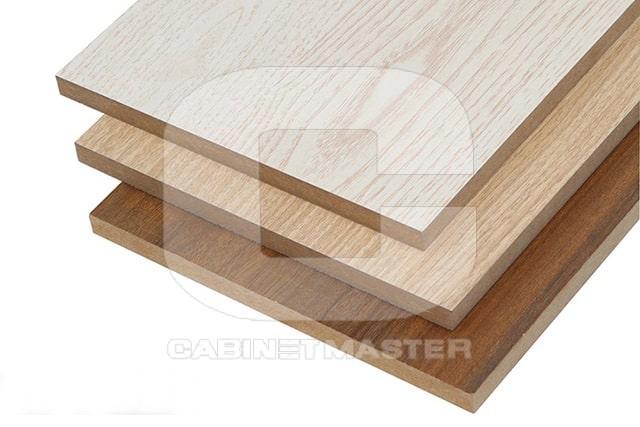
3.4 Kích thước
Những tấm gỗ HDF thường có kích thước thông thường là 2.000 mm x 2.400 mm. Nó được sản xuất với độ dày từ 6mm đến 24mm, tùy thuộc vào yêu cầu cụ thể.
3.5 Ưu nhược điểm
Về ưu nhược điểm thì HDF có những đặc điểm sau:
- Ưu điểm: Ưu điểm của Gỗ HDF bao gồm khả năng cách âm tốt, chịu nhiệt cao, phù hợp cho sản phẩm nội thất phòng học và phòng ngủ. Ván HDF có khung gỗ xương ghép công nghiệp chống mối mọt và khắc phục nhược điểm của gỗ tự nhiên. Độ đa dạng màu sơn, bề mặt nhẵn bóng và khả năng chống ẩm tốt là những ưu điểm nổi bật của loại gỗ này.
- Nhược điểm: Nhược điểm của Gỗ HDF bao gồm khả năng chống thấm nước kém, độ dày và độ dẻo dai hạn chế. Một số loại gỗ có thể ảnh hưởng đến sức khỏe người sử dụng. Đồng thời, gỗ HDF cũng không thể chạm trổ được các chi tiết cầu kỳ như gỗ tự nhiên.
3.6 Ứng dụng
Gỗ công nghiệp HDF là một giải pháp tốt cho đồ nội thất trong và ngoài trời, tấm tường, đồ nội thất, vách ngăn văn phòng và cửa ra vào. Ngoài ra, loại gỗ này còn được sử dụng làm sàn gỗ, tủ bếp do tính ổn định và mật độ mịn. Bên cạnh đó, gỗ công nghiệp HDF này được ưa chuộng vì tính thân thiện với môi trường và giá thành hợp lý, không gây hại cho sức khỏe người sử dụng.
>>>> XEM THÊM: So sánh HDF và MDF – Ưu nhược điểm từng loại gỗ, loại nào tốt
4. Gỗ ép (Plywood)
Gỗ ép cũng là vật liệu được ưa chuộng trong nhiều công trình xây dựng và nội thất do tính linh hoạt và độ bền cao. Cách phân biệt các loại gỗ công nghiệp – Gỗ ép như sau:
4.1 Phân loại và cách phân biệt các loại gỗ công nghiệp ép
Các dòng gỗ ép thường được phân loại dựa trên chất liệu cấu thành, chống nước, chịu nhiệt và mục đích sử dụng. Một số loại phổ biến bao gồm gỗ ép công nghiệp, gỗ ép chống nước và gỗ ép chịu nhiệt. Các tính chất cụ thể của gỗ ép phụ thuộc vào loại keo và chất phủ được sử dụng trong quá trình sản xuất. Cách phân biệt các loại gỗ công nghiệp ép cũng có thể nhận biết chúng thông qua nhãn hiệu, thông số kỹ thuật kỹ thuật hoặc thông tin của nhà sản xuất.
4.2 Nguyên liệu cấu thành
Các dòng gỗ ép có thể được phân loại dựa trên nguyên liệu cấu thành, loại keo, và chất phủ. Dưới đây là một số nguyên liệu cấu thành chính của gỗ ép:
- Gỗ Tự Nhiên: Gỗ tự nhiên như gỗ thông, gỗ sồi, hay các loại gỗ khác có thể được sử dụng làm lớp nền cho gỗ ép. Các loại gỗ này thường được chọn vì tính chất cơ học và tính thẩm mỹ của chúng.
- Bánh Gỗ (Veneer): Bánh gỗ là lớp mỏng được cắt từ một tảo gỗ tự nhiên và được sử dụng để tạo ra bề mặt bảo vệ cho gỗ ép. Điều này cũng là ưu điểm của ván Veneer về độ bền cao hơn các dòng ván gỗ khác.
- Keo: Keo là yếu tố quan trọng giữ chặt các lớp gỗ lại với nhau. Có nhiều loại keo khác nhau, bao gồm keo UF (urea-formaldehyde), keo MUF (melamine-urea-formaldehyde), và keo PF (phenol-formaldehyde). Sự lựa chọn của keo ảnh hưởng đến đặc tính cơ học và chống nước của gỗ ép.
- Chất phủ: Chất phủ bảo vệ bề mặt của gỗ ép khỏi ẩm, mài mòn, và tác động của môi trường. Các loại chất phủ phổ biến bao gồm sơn, gốm, và các chất phủ chống nước.
- Vật liệu tái chế: Một số sản phẩm gỗ ép sử dụng nguyên liệu tái chế, giúp giảm tác động tiêu thụ nguồn tài nguyên tự nhiên.
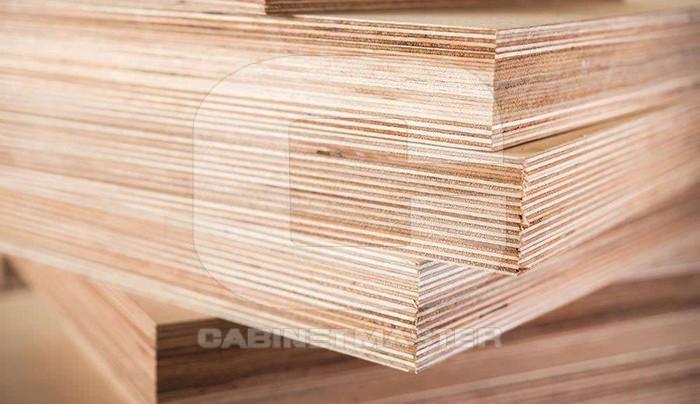
4.3 Quy trình sản xuất
Quy trình sản xuất gỗ ép bao gồm các bước chính sau:
- Chuẩn bị nguyên liệu: Nguyên liệu cần được chuẩn bị, bao gồm gỗ tự nhiên, bánh gỗ, keo, chất phủ, và vật liệu tái chế (nếu có).
- Cắt gỗ: Gỗ tự nhiên và bánh gỗ được cắt thành các tấm có kích thước và độ dày mong muốn. Sau đó kết hợp chúng lại với nhau theo từng lớp.
- Làm sạch và tiền xử lý: Bề mặt gỗ được làm sạch và tiền xử lý để loại bỏ bụi bẩn, dầu, và các chất khác trước khi áp dụng keo.
- Áp dụng keo: Keo được áp dụng đều lên bề mặt gỗ để kết nối các lớp lại với nhau. Loại keo được sử dụng có thể ảnh hưởng đến đặc tính của sản phẩm cuối cùng.
- Ép và nung sấy: Các lớp gỗ được ép lại với nhau và sau đó nung sấy để keo cứng lại và tạo ra một sản phẩm gỗ ép chắc chắn.
- Chuẩn bị bề mặt và áp dụng chất phủ: Bề mặt của gỗ ép được chuẩn bị và sau đó áp dụng chất phủ bảo vệ như sơn, gốm, hoặc chất phủ chống nước.
- Kiểm tra chất lượng: Sản phẩm được kiểm tra chất lượng để đảm bảo đáp ứng các tiêu chuẩn cụ thể về cả tính chất cơ học và mỹ thuật.
- Đóng gói và xuất xưởng: Sản phẩm gỗ ép được đóng gói cẩn thận trước khi xuất xưởng để bảo đảm an toàn và tiện lợi trong quá trình vận chuyển và sử dụng.
4.4 Kích thước
Kích thước của gỗ ép thường phụ thuộc vào mục đích sử dụng cụ thể và yêu cầu của dự án. Thông thường, các tấm gỗ ép có kích thước tiêu chuẩn như 4×8 feet (1220x2440mm) hoặc 5×10 feet (1525x3050mm). Tuy nhiên, có thể có các kích thước tùy chỉnh để đáp ứng nhu cầu cụ thể của khách hàng.
4.5 Ưu nhược điểm
Ưu điểm:
- Độ bền: Gỗ ép thường rất bền và chịu được áp lực cao.
- Ứng dụng rộng rãi: Có thể sử dụng trong nhiều lĩnh vực từ xây dựng đến nội thất.
- Tính chất cơ học tốt: Có khả năng chịu uốn, xoay và uốn cong tốt.
Nhược điểm:
- Chống nước: Một số loại gỗ ép có khả năng chống nước hạn chế.
- Môi trường: Quá trình sản xuất có thể tạo ra chất thải môi trường.
- Giá cả: Một số loại gỗ ép chất lượng cao có giá cao.
4.6 Ứng dụng
Ứng dụng của gỗ ép như sau:
- Xây dựng: Gỗ ép được sử dụng rộng rãi trong xây dựng như làm ván sàn, cột và kết cấu nhà.
- Nội thất: Sản phẩm gỗ ép thường được sử dụng trong việc làm nội thất như tủ, bàn, và ghế.
>>>> BÀI VIẾT LIÊN QUAN: So sánh giá Veneer và Laminate, Melamine – Chọn vật liệu nào?
5. Gỗ nhựa (Gỗ công nghiệp kết hợp bột nhựa)
Gỗ nhựa là loại vật liệu kết hợp gỗ tự nhiên và nhựa. Để tìm hiểu về gỗ nhựa và cách phân biệt các loại gỗ công nghiệp nhựa, CABINETMASTER mời bạn cùng theo khảm các thông tin dưới đây:
5.1 Phân loại và cách phân biệt các loại gỗ công nghiệp nhựa
Gỗ nhựa có thể được phân biệt thông qua kiểu mẫu và màu sắc của bề mặt. Đồng thời, gỗ nhựa thường được sản xuất với lớp nhựa phủ bóng nên bề mặt sáng và mịn màng rất đẹp. Các chi tiết kỹ thuật như độ dày và cấu trúc cũng có thể giúp bạn phân biệt gỗ nhựa nhưng sẽ hơi khó. Cách phân biệt các loại gỗ công nghiệp – gỗ nhựa và loại phổ biến hiện nay:
- Gỗ Nhựa Composite: Kết hợp gỗ và nhựa, cung cấp độ bền cao và chống nước.
- Gỗ Nhựa PVC: Sử dụng nhựa PVC, chống nước, chống mối mọt.
5.2 Nguyên liệu cấu thành
Nguyên liệu chính của gỗ nhựa là nhựa và gỗ tái chế. Quá trình sản xuất thường bao gồm việc kết hợp 2 nguyên liệu chính và dùng máy móc để xử lý chúng, từ đó tạo ra sản phẩm cuối cùng. Cụ thể quy trình sản xuất mời bạn xem tiếp mục dưới đây.
5.3 Quy trình sản xuất
Quy trình sản xuất gỗ nhựa thường bao gồm các bước chính sau:
- Nguyên liệu:
- Gỗ tái chế: Sử dụng gỗ từ nguồn tái chế giúp giảm áp lực đối với nguồn gỗ tự nhiên.
- Nhựa: Sử dụng các loại nhựa phù hợp, thường là nhựa tái chế hoặc nhựa PVC.
- Chuẩn bị gỗ: Gỗ được cắt thành các tấm nhỏ với kích thước và hình dạng cần thiết cho quy trình sản xuất.
- Xử lý gỗ:
- Gỗ được xử lý để loại bỏ ẩm và các tác nhân gây hại khác.
- Áp dụng các chất phủ chống mối mọt và chống nước nếu cần thiết.
- Chế tạo lớp nhựa:
- Nhựa được chuẩn bị và gia nhiệt để tạo thành lớp nhựa chất lượng cao.
- Lớp nhựa này sau đó được áp dụng lên các tấm gỗ thông qua quá trình ép nhiệt.
- Ép nhiệt và kết hợp:
- Gỗ và lớp nhựa được ép lại với nhau dưới áp suất và nhiệt độ cao để tạo ra sản phẩm cuối cùng.
- Quy trình này giúp kết hợp tính chất cơ học của gỗ và khả năng chống nước của nhựa.
- Cắt và hoàn thiện:
- Sản phẩm được cắt thành kích thước và hình dạng cuối cùng.
- Áp dụng các công đoạn hoàn thiện như mài, làm bóng, hoặc thêm lớp phủ bảo vệ.
- Kiểm tra chất lượng: Sản phẩm cuối cùng được kiểm tra chất lượng để đảm bảo đáp ứng các tiêu chuẩn và yêu cầu.
- Đóng gói và vận chuyển: Sản phẩm được đóng gói và chuẩn bị cho quá trình vận chuyển đến các địa điểm sử dụng.
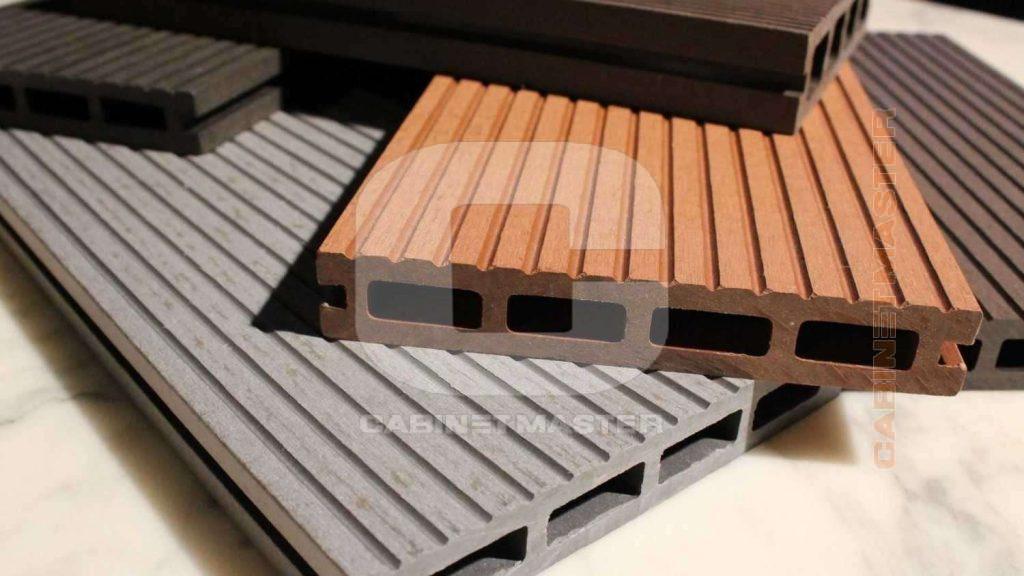
5.4 Kích thước
Kích thước của gỗ nhựa thường được sản xuất theo các tiêu chuẩn cụ thể tùy thuộc vào ứng dụng. Gỗ nhựa có thể có độ dày và kích thước chiều rộng, chiều dài khác nhau, tùy thuộc vào mục đích sử dụng trong xây dựng, nội thất.
5.5 Ưu nhược điểm
- Ưu điểm của gỗ nhựa:
- Chống nước: Gỗ nhựa thường có khả năng chống nước. Điều này giúp gỗ nhựa phù hợp với các ứng dụng trong môi trường ẩm.
- Dễ dàng bảo quản: Gỗ nhựa không yêu cầu bảo quản chống mối mọt và không bị ảnh hưởng bởi môi trường nước biển.
- Nhược điểm của gỗ nhựa:
- Độ bền không cao như gỗ tự nhiên: Gỗ nhựa không có độ bền tự nhiên cao như gỗ thật.
- Khả năng tái chế hạn chế: Một số loại gỗ nhựa khó tái chế, ảnh hưởng tiêu cực đến môi trường.
5.6 Ứng dụng
Ứng dụng của gỗ nhựa như sau:
- Nội thất ngoại thất: Sản xuất đồ nội thất như bàn, ghế, sàn nhựa.
- Xây dựng: Sử dụng trong vách ngăn, cửa, sàn nhựa.
- Đóng gói: Tạo pallet, hộp đựng hàng hóa.
Bài viết này đã chia sẻ cho bạn cách phân biệt các loại gỗ công nghiệp: MFC, HDF, MDF, Gỗ ép, Gỗ nhựa. Hy vọng bạn sẽ biết thành thạo cách phân biệt các loại gỗ này. Đừng quên luôn theo dõi CABINET MASTER để biết thêm nhiều kiến thức và kinh nghiệm hữu ích về các loại gỗ cũng như máy móc hiện đại phục vụ cho sản xuất nội thất nhé!
>>>> ĐỪNG BỎ LỠ: